出庫とは?出荷との違いや効率化のポイントまで徹底解説
出庫とは、倉庫などの保管拠点から商品や資材を出して出荷先へ搬出する一連の業務を指します。ECの拡大や即日配送のニーズが高まる中、出庫業務の効率化と正確性は、企業の競争力を左右する重要な要素となっています。本記事では、物流施設の開発・運用に強みを持つシーアールイーが、出庫業務の基本から効率化のポイントまで、業界に精通した視点でわかりやすく解説します。
出庫とは?
出庫は、倉庫内で保管している場所から外へ出す作業を指します。倉庫内にはさまざまな場所に多種多様な在庫が置かれているため、正確な保管場所の把握と正しいピッキング手順が不可欠です。
出庫時には、数量や商品カテゴリだけでなく、ロットや消費期限の管理も行われるケースがあります。これらを間違えると、本来運ぶべき商品と異なるものが出荷されるなどのトラブルを引き起こすため、出庫は非常に重要な工程の一つです。
出庫と入庫の違い
入庫は倉庫で商品や材料を新たに受け入れ、保管場所に格納する工程(棚入れとも呼ばれます。)であり、在庫を増やす工程です。一方、出庫は倉庫にある在庫品を外へ出す作業で、在庫を減らすという側面を持ちます。
適切なデータ管理がされていれば、商品のロスや過剰在庫を防ぐことができます。入庫と出庫がお互いにどのように連動しているのかを理解し、システム管理と現場の作業手順をリンクさせることがポイントです。
出庫と出荷の違い
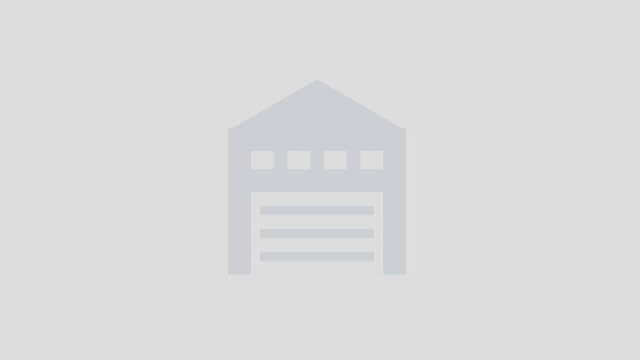
よく間違えがちなのが、出荷と出庫の違いです。出庫は倉庫内で商品を取り出す行為そのものを指すのに対し、出荷は、出庫した商品を顧客や配送先へ届ける工程全体を含みます。つまり、出庫は出荷という大きな工程の一部ということになります。
みなし出庫とは
みなし出庫とは、物理的に倉庫から商品が移動していなくても、在庫管理上は出庫したと見なす処理を行うことです。
機械製品や車など多くの部品を扱う工場などでよく使う管理方法のひとつです。例えば工場の場合、部品が多くあるのにパーツを組み立てるたびに部品の出庫伝票を発行していたら膨大な作業量になることが予想できます。こうしたケースにみなし出庫を行うことで効率化を図るということです。
この方法を活用することで、現場で伝票を都度発行するといった負荷を軽減し、在庫データを分かりやすく整理することが可能です。ただし、みなし出庫のタイミングや記録のルールを明確にしないと、在庫情報にズレが生じ、誤発注や欠品の原因につながります。
出庫で起こるミスと注意点
出庫は多くの手作業や人的判断が求められるため、ミスが起こりやすく、また発生時に気づきにくい工程でもあります。
出庫作業では、商品の選別や数量確認、検品などを人手で行う場面が多いのが実情です。それに加えて、現場によってはみなし出庫を行っていると、商品を間違える、数量を誤る、伝票と実在庫を照合しないなどのヒューマンエラーが起きやすくなります。
ただしこれらは運用の中でエラー箇所を的確に押さえ、一つ一つ対応することで改善することができる事象です。
ピッキングミスや検品ミス
ピッキングミスや検品ミスは、現場作業が複雑になるほど増える傾向にあります。そのため、作業工程の標準化、ミスした場合の検知箇所の設計が必要不可欠です。
特に在庫数や残数をリアルタイムで把握できない環境では、二重で確認を行うなどの追加対策を講じることが求められます。誤出荷が起きると、返品対応や再発送などのコストが生じるだけでなく、顧客満足度にも大きな悪影響を与えてしまいます。
検品やピッキングの段階で照合を行う仕組みを導入し、作業者が目で見て確認できるようなラベルやバーコード管理を併用すると、人的ミスのリスクを大幅に削減できます。
運用ルールの設定と遵守
出庫作業の現場は、担当者や業務量によって作業品質や手法にばらつきが出やすい部分でもあります。誰が担当しても一定の品質を保てるよう、確立したルールを設定することは重要です。
例えば、チェックリストやマニュアルを作成し、出庫の各ステップで必ず行うタスクを明文化します。これにより、作業手順が属人的にならず、複数の担当者でカバーする際にも安定したパフォーマンスを発揮しやすくなります。
また、実際の作業負荷や新しい取り扱い商品の追加に合わせてルールを見直し、常に最適化を図ることで、継続的に出庫精度を高めていくことができます。
出庫業務を効率化させるポイント
出庫作業をさらにスムーズに進めるためには、倉庫レイアウトやシステムの活用方法を見直すことが効果的です。ここでは、実務で役立つ具体的な改善のヒントを紹介します。
ピッキングしやすい保管場所の設置
出庫頻度の高い商品は、短い動線で取り出せる位置に配置するのが基本です。作業者にとって動きやすく、手が届きやすい高さと場所に最も回転の速い在庫を集約しましょう。
この際に注意したいのは、作業者ごとの体格の違いや使用器具によって取りやすい場所が微妙に変わることです。複数の作業者にヒアリングを行い、誰にとっても無理の少ないレイアウトに調整するのがおすすめです。1回1回の作業の積み重ねによって疲労も蓄積し、ミスも誘発してしまうからです。
視認性、作業性が高い場所に商品を置くことで、誤ったものを選んでしまうリスクが低減します。
ロケーション管理の見直し
ロケーション管理とは、倉庫内のどこに何があるのかを一目でわかるように整理・番号付けする仕組みです。適切に設定されたロケーション情報があれば、必要な商品を素早く見つけてピックアップできます。
棚番やエリア分けのルールが曖昧だと、初めて働く作業者も覚えにくく混乱を招きやすくなります。
倉庫管理システム(WMS)の導入
倉庫管理システム(WMS)を導入することによって、入庫から出庫までの全工程をデジタルで一元管理できます。特に出庫工程では、ピッキングリストの自動作成やリアルタイムの在庫管理機能が大いに役立ちます。
システムを介して作業者がピッキングを行い、完了登録をすることで、在庫数や位置情報が即時に更新されるため、作業者間での伝達ミスを防止できます。特に大量の商品を扱う倉庫においては、高い効果が期待できます。
出庫作業の自動化とAI技術の活用
近年では、ロボットによるピッキング作業や自動仕分けシステムなどの導入が進んでおり、人手不足や人為的ミスの削減に大きく寄与しています。画像認識技術やAIを用いた検品も、正確性を高める上で注目されています。たとえば、1966年に冷蔵倉庫事業を開始し、1974年には今日まで続く冷凍食品メーカーの共同配送事業を始めた株式会社ヒューテックノオリンでは、2024年時点、全国13施設に自動倉庫を導入しており、同社の保管パレット数でみて約5割をフォークリフトや人の介在なしで入出庫可能にしています。
ただし、高度なシステムを導入するにはコストや導入期間の問題もあります。自社の物流規模や取り扱い商品の性質に合わせて、段階的にシステムを拡張していくのが現実的な選択肢といえます。
まとめ
近年、物流業界における荷物量は増加の一途を辿っており、物流現場ではより効率的かつ正確に荷物を運ぶことが求められています。出庫業務は物流の流れにおける重要な要素のひとつであり、効率化し、ミスを最小限に抑えることは、自社の物流の品質向上につながります。そのため、倉庫運営においては、適切なルールの策定と最新技術の導入を検討し、継続的な改善を図ることが重要です。
シーアールイーが運営するサイト「CRE倉庫検索」では、各社の物流課題への取り組みを独自取材したインタビュー記事など物流課題の解決のヒントとなる情報も豊富に掲載しておりますので、ぜひご覧ください。