大手卸・あらた現場ベテランに聞く改革の舞台裏|物流クロスオーバー【日雑シリーズ 卸編】
自動化推進の積極策で成果、メーカーとの連携進展も、小売との連携に課題
連載インタビュー記事「物流クロスオーバー」
「物流企業と荷主業界の垣根をクロスオーバーした相互理解と問題解決を支援し、産業界全体の発展に寄与する」ことをパーパスに掲げた話題の企画、「物流クロスオーバー」。日用雑貨物流シリーズの第4回目は、集約の進む日雑卸分野から、業界のもう一翼を担う「あらた」社にご登場いただきました!
同社は2019年の最も早い時期に「ホワイト物流」推進運動の自主行動宣言を発出し、入荷予約システムの積極採用やメーカーとの間でのASNデータ送受信など施策を着々と進行。物流2024年問題への対応準備をいち早く進め、成果を挙げてきました。では残る課題と、次の一手は何か? あらたの物流現場を長年担い続けてきた大ベテランであるロジスティクス本部の今井達也氏にホストの菊田がしつこく迫り、ホンネを聞き出します。ぜひご一読ください!
(インタビュー・企画構成/エルテックラボ 菊田一郎)
今回のゲスト |
株式会社あらた ロジスティクス本部 横浜センター駐在 今井達也氏 株式会社あらた |
---|
約10万アイテムの商品の納品精度は99.999%
株式会社あらた
ロジスティクス本部 横浜センター駐在 今井達也氏
私は過去10年ほど、貴社の物流について繰り返し取材させていただいてきたのですが、今回は改めて、貴社ビジネスの最新状況を教えてください。
今井氏 当社は日用品・化粧品分野において、日本最大級の規模を持つ卸商社です。小売業とメーカーをつなぎ、情報を一元管理して消費者の皆様へ商品を届けるお手伝いをしています。取引先のメーカーは約1,200社で、取扱商品は約10万アイテムに上ります。また販売先である小売業はドラッグストア、ホームセンター、スーパー、ディスカウントストア、GMS、Eコマースなど約3,500社・約4.5万店舗で、様々な情報や地域、季節、流行などに合わせた販促企画、付加価値とともに商品をお届けしています。2024年3月期の売上は9,441億円といよいよ1兆円の大台目前となり、気を引き締めているところです。
取扱商品をカテゴリー別にみると、ヘルス&ビューティーが30.7%、ハウスホールド品が14.2%、ホームケアが8.0%、紙製品が19.4%、家庭用品が6.7%、ペット・その他が21.0%あります。ペット関係はグループ企業のジャペル(株)が取り扱っているものですが、この分野は近年すごい勢いで伸びていて、中でも健康など付加価値のある高単価商品が売れているんです。
ペット用品の物流もあらたに一体化しているのですか?
今井氏 ペットの物流はあらたでも一部取り扱っていますが、主にジャペルが独自に行っており、今後はさらなる全体最適化に取り組んでいくことも検討しています。
現在の物流拠点ネットワークは、全国7支社で北海道から九州まで、年間出荷額150億円以上の大型物流センターを中心に31か所の自社物流拠点を持ち、別にコスメの専用センター3拠点、デポ5拠点があります(図表1)。この他に外部委託倉庫が裾野に多数あります。
売上構成比はドラッグストアが50%強で、ホームセンターが14%、と続きます。これらのお客様に約10万アイテムの商品をお届けする際の納品精度は、99.999%。ファイブナインを目指して頑張っているところです。
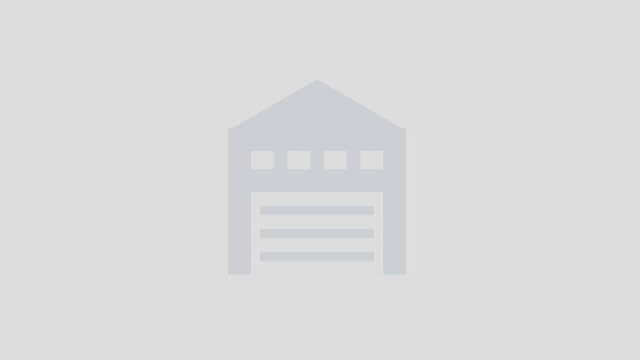
物流センター作業の自動化を積極推進
以前、貴社の江南センター、鹿児島センターほかの現場取材に伺いまして、最新鋭の自動化設備機器の導入に努力を続けてこられた経緯を存じています。一方、鹿児島ではAIケースハンドリングロボット(デパレタイザ)が活躍していたのが強く印象に残っています。
今井氏 はい、以前から自動化設備は各地の物流センターに積極的に導入してきました。パレット自動倉庫(写真1)は重量品も多い日用品のハンドリングには欠かせず、業界標準のT11型パレットに積載して、自動で搬送・格納・出庫・在庫管理を行っています。
鹿児島でご覧になったAIデパレタイズロボットは、メーカーよりパレット単位で入荷した商品から、小売業へ納品するケース単位で自動ケースピッキングします。ロボットは3D・2Dの3台のカメラで商品を認識し、今日初めて扱う商品でも正確に認識してエア吸着でピックし、搬送コンベヤに移載します。能力は最大450ケース/hで、夜中の無人作業も可能です。
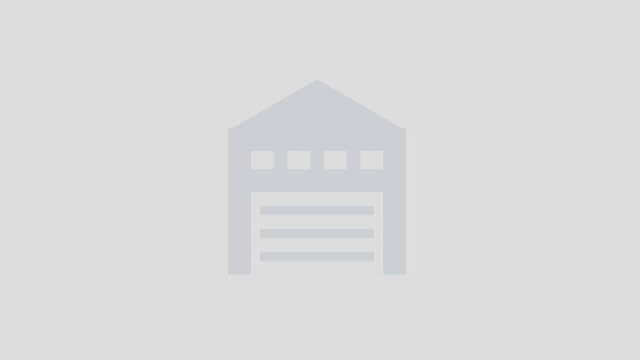
以前取材した時に責任者の方から、段ボール箱の強度が不十分で、上面からロボットで吸着すると破損してしまうものがあるのが悩みだと聞きました。
今井氏 ええ、そうだったんです。そこでロボットメーカーが工夫してくれ、昔は天面だけをエアで吸着していたのを、今ではハンド部分をL字型にし、側面と天面の2方向から吸着することで、破損がかなり回避できるようになりました。ロボットは常に安定したパフォーマンスを発揮してくれます。
残る課題がバラの小分けピッキング作業で、これについて当社は独自のピッキングカートシステム「AiMAS(アイマス)」を開発し、進化させてきました。①商品バーコードをスキャンすることで「商品違い」を、②電子秤による重量検知(1グラム単位で検量し商品マスタデータと照合)で「数量違い」を、③どの秤が検知したかで「納品先違い」をなくし、オリコンに投入することで、納品精度99.999%の超高精度な出荷を実現しています。
アイマスはパートさんがカートを押して歩き、システムの支援で効率的にピックする半自動化システムですが、最近話題のAMR(自律搬送ロボット)の導入も検討されていますか?
今井氏 はい、まさに今、それを探求しているところなのです。ロボットメーカーがいろいろなAMR製品を出していて、それだけ見ると良い機能が一杯あるように思えるのですが、いざ当社センターに実際に導入できるかとなると、なかなかピッタリの機種がない。卸の物流現場に一番よいものは何か?専門部署が研究しています。でも技術はどんどん進化していますからね。
たとえばアイマスでも、当社では腕に付けられる小型の補助端末「アイマス モバイル」を用意し、カートが混み合った場合など、作業者がカートから離れてピッキング指示を見て作業できる仕組みにしているんです(写真4))。
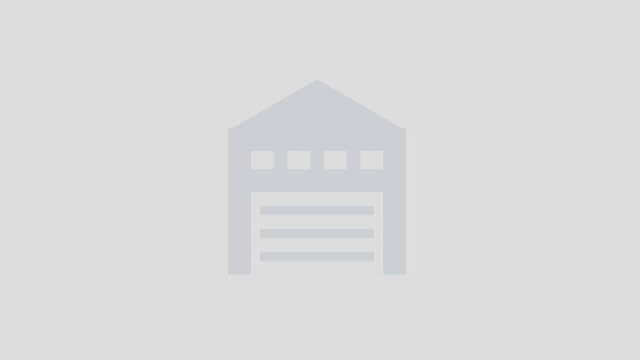
渋滞や手待ちが発生すると、せっかくのシステムの生産性が落ちてしまいますからね。集中・渋滞回避のために、棚の商品ロケーションのメンテナンスなども行っていますか?
今井氏 はい、常にロケーション管理をしています。
次がオリコン自動倉庫(写真5)で、これは受注が五月雨式に入るのに対し、納品時間はお客様ごとに違うので、アイマスでピックした出荷用のバラ品オリコンを一旦ここに保管し、企業別・配送ルート別・店舗別などに順立てしまとめ、高速で払い出すシステムです。これにより店違い等の誤配送をなくし、仕分け時間やスペースを削減することができます。
もう1つがピースソーターです(写真6)。日用品・化粧品業界では夏の殺虫剤、冬のカイロや入浴剤など季節商品も多く、かなりの返品が発生します。店舗から戻ったそうした返品商品の扱いはとても煩雑なのですが、このソーターに投入すればメーカー別・カテゴリー別・商品単品別に自動的に仕分けて、伝票も挙げてくれます。
物流課題解決に向けた取り組み①入荷予約システム
なるほど、現場取材で拝見した多様な物流現場作業の効率化システムを改めて認識させてもらいました。こうしたセンター構内の取り組みに加えて、近年叫ばれている物流課題への対応も、貴社は早い時期から進められてきたようです。
今井氏 そうですね。物流現場の効率化だけでなく、社会全体の物流課題解決にも積極的に取り組んでいますので、代表的な取り組みをいくつか抜粋してご紹介します。まず当社は<「ホワイト物流」推進運動の自主行動宣言>を2019年7月に提出しました。ご存じのように「ホワイト物流推進運動」とは、深刻化が続くトラック運転者不足に対応し、国民生活や産業活動に必要な物流を安定的に確保するとともに、経済の成長に寄与することを目的とした運動です。国土交通省・経済産業省・農林水産省が推奨する運動の趣旨に賛同し、物流の効率化・トラックドライバーの待機および荷役時間の削減に向けて自主的に行動する宣言を行いました。
まずTSUNAGUTE社の入荷予約システムを導入することを決め、同年から全国の拠点に順次採用し、ドライバー不足の1つの要因とされるトラックの待機時間削減を目指しました。
実はこのシステム(写真7~9)を初めて導入したのは、私が担当していた愛知の江南センターだったんです。当時の江南センターは最大でトラックを4時間も待たせるなど待ち時間が長く、ドライバー他からいつもお小言を頂戴していました。朝一番に納品作業を始めたいトラックが夜中から行列を作っていますが、接車バースは5か所しかなく、すぐにその枠が埋まるとまた長時間待たねばならない。何台もトラックが並び、交通整理もできない状態でした。
私も何とかしなければと思っていたので、予約システムを一番に導入しました。入荷の5日前から予約できるようにし、配車が決まり次第、予約を入れてもらいます。
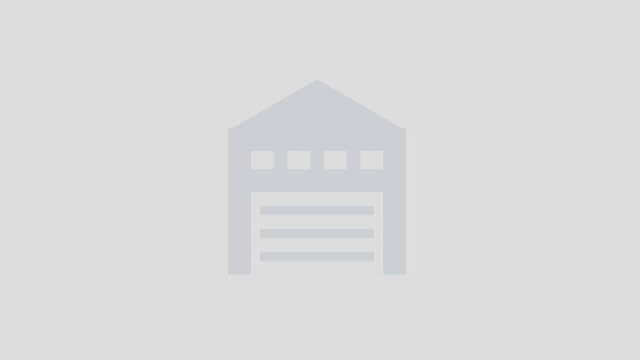
でも配車が決まるのは前日とかの直前では?
今井氏 1日前、2日前が多いのですが、先行注文を出していれば早期に配車を組めるものもあるんです。ただし簡単には行きませんでした。そもそも1日に入荷できるキャパシティに合わせて台数を計算し、予約できる枠を作らないと、溢れてしまうことが間もなく分かったんです。繰り返し枠の設定と台数を調整し続け、やっと使える仕組みにできました。
受発注には商流上の判断も絡むので、難しいところがあるんです。「売上を確保したい」との意図や、欠品が出ないように先々の分まで確保したい思いなど、製販双方の販売・調達部門の事情が優先されると、センターでは過剰な納品を受け、トラックが列を作り、在庫が満杯になってしまったりするんです。
物流部門が他部門をコントロールして在庫の適正化、需給の最適化を主導することは難しい。それはロジスティクス部門長、CLO(最高ロジスティクス責任者)の役割ですよね。本シリーズではサンスター社が、メーカーの長期休暇前の物流波動問題に着目し、年末の休み前に1日稼働日を増やす実験を行ったところ、山を崩して半分にできたと話してくれました。
今井氏 夏のお盆休みに、メーカーは最長で10日間ほど休みます。単純計算では、物流センターはその10日分の在庫を休み前に入荷しないといけないわけですが、一度に納品されたら受け入れられるわけがありません。それでトラックが長時間滞留し荷主責任が問われたら、当社は物流2024年問題対応がアウトになってしまいますから、放置できないんです。
メーカーの会社は休みになっても、サンスター社のように配送だけ動かしてくれればいいと思いますが、そうは行かないものですか?
今井氏 対応してくれるメーカーもありますが、少ないですね。連休の真ん中に1日だけでも動かしてくれれば、ものすごく助かるんですが。我々卸売業は365日稼働ですから、せっかく導入した予約システムをうまく活用して改善できればと思います。
予約システムの導入数は、4年間頑張った結果、2024年6月時点で29拠点まで拡大しています。6月までの導入効果をまとめると、下のようになります。
------------------------------------------------------------------------------
①予約入荷構成比 対象拠点(28拠点)の平均構成比---------67%
②利用トラック台数 対象拠点(28拠点)の月合計台数平均-----7,080台
③待機時間平均 対象拠点(28拠点)の月平均待機時間-----16分
-------------------------------------------------------------------------------
導入拠点では70%弱の物量が予約入荷になり、利用トラック台数は月に約7,000台。待機時間は導入拠点平均で「16分」になりました。
16分!素晴らしい成果ですね、「最長4時間」だったのが!
今井氏 数字としてはっきり表れてよかったです。いやあ、難しかったですけれどね。かつての江南センターのようなひどい待機のストレスは、もうありません。今般成立した改正総合物流効率化法で、「待ち・荷役時間は1運行当たり2時間以下」のルールが設定されました。発荷主であるメーカーの出荷時に1時間かかっていると仮定して、受荷主である当社も「1時間以内」にすることを目指しています。細かい実績データも取っていますが、現在ではほぼ1時間以内にできています。
私があちこちの当事者にヒアリングしたところ、卸業界でもこれを「発着合わせた1運行で2時間」ではなく、「発で2時間、着で2時間」と理解している企業もあったんです。でも法律の条文は明らかに前者を意味しているらしい。だとするとこの場合、正確に1運行で2時間以下だったことを確かめるためには、その便の出荷時にメーカーが何分かけて積んだかのデータを卸が手に入れて突合し、証明しないといけなくなりませんか?
今井氏 もし、今日はメーカーの出荷で1時間20分かかったから、当社の残り時間は40分しかない……なんてことになったら困りますね。
専門家に確認したところ、荷主にそんなデータ収集の負担を新たにかけることはなく、「発で1時間、着で1時間」以内を目指して取り組む方向になりそう、とのことでした。
物流課題解決に向けた取り組み②ASNデータ送受信
メーカー、卸・物流センター双方への取り組みがあれば教えてください。
今井氏 もう1つの取り組みは、メーカーとの間でASN(事前出荷情報)データの送受信を開始したことです。これによる成果としては、以下の点が挙げられます。
<メーカーの導入効果>
・納品書レス(納品明細・伝票)
・事務作業の効率化(受領書管理)
・ドライバーの拘束時間短縮(2024年問題対応)
<卸・物流センターの導入効果>
・入荷検品簡素化による人件費削減
・欠品の早期把握と対処
・事務作業の効率化(納品書管理)
・期限管理品の入力作業軽減
・配送車両情報の早期把握(ASN2.0)
・格納作業の効率化(ただし、フロア別表示が必要)
ASNの導入は2024年2月に開始し、この6月末時点で14拠点に導入を完了、7月中にさらに8拠点へ導入予定です。実際、我々もストレスなく入荷を行えるようになりました。
実はASNには数段階のレベルがあります。従来は伝票の発注ナンバーを手作業で拾ってあちこちに散らばっている入荷商品と照合し、全部足し合わせて初めて、正しく納品されたかどうかが分かる流れだったのが、その手間がなくなるのが基本的なASNの効果です。
それがトラック1台目に何が何ケース、2台目には何が何ケースと、車単位でデータが届くのが、Ver2。これでドライバーは早く帰れるようになりますが、卸の物流センター側は納品された商品を格納しなければなりません。最終的に目指すのは、当社の格納ロケーションともデータ連携して、もっとバースの回転を速める取り組みが必要です。ASNで言えばユニットロード単位がVer3、バース予約まで連携するのがVer4ということになります。
しかしわずか半年余りで22拠点に導入とは、すごいスピードですね。
今井氏 はい、日雑業界の共同物流会社として機能していた旧プラネット物流の利用メーカーが主体となったことで、急速に進みました。
物流課題解決に向けた「チャレンジ」事例
この他に物流課題に向けての取り組みがあれば教えてください。
今井氏 以上の大きな取り組み以外に、この間チャレンジしてきた事例を簡単に紹介します。
①パレット納品への取り組み……手積み・手下ろし入荷をパレット化し効率化
これは15年ほど前からの取り組みで、紙おむつメーカーがそれまで、パレットなしに手積みで満車にして納品されていたため、発着でそれぞれ荷下ろしに1時間半ずつかかっていました。そこで同社にお願いしてパレット化に対応していただいたことで、積み下ろしとも数十分で済むようになりました。ただし積載率が下がるので、運送会社が近場に積み替え拠点を設け、ここでパレットに積み替えて納品し、回転率でこれをカバーする方式にしています。
②入荷時間枠の緩和……入荷受付時間を夕方まで延長しトラックの有効活用
以前は午前中に納品が集中し混雑していたので、夕方から夜まで納品可能な時間枠を広げる対応を江南センターで開始しました。これでそのトラックは午前中に別の荷物を運んで戻ってから、午後に当社に納品すればよくなりました。入荷予約システムの前身ともいえます。
③小・中ロット入荷メーカー集約入荷……2017年、分散入荷トラックの集約化、ミルクラン
荷量が小さく、小ロット・中ロットの入荷しかないメーカーもあり、積載率の低い配送車両が多数来る状態になっていました。そこで当社の方がトラック便を立て、ミルクラン方式でまとめて集荷するように考えたものです。車は1台で済むし、コントロールもしやすく、多くのメーカーに参加してもらえれば安い運賃にできるはずでしたが、当時はまだ危機感が低くて参加メーカー数が揃わず、定着させられませんでした。今ならできるかもしれないので、改めて仕掛けようと思っています。
④格納先別パレタイズ入荷……2018年2月、サンスター社と共同で取り組みを実施
サンスター社と一緒に行った事例で、当社の格納ロケーションデータを事前にお伝えし、グループに分けてパレタイズし、納品してもらうようにしました。これで納品を受けたらすぐに棚入れでき、大きく効率化できました。この事例は内閣府で当時の安倍総理を前にサンスター社が報告されましたが、私も同行し、初めて首相官邸に入れてもらって感激しました(笑)。
⑤中部運輸局との取り組み……2019年3月、「トラック輸送における引取環境・労働改善協議会におけるコンサルティング事業」取り組み
中部運輸局から、付帯作業も含めてもっと物流の実態を分析してくれないかと依頼があり、当社とホームセンター、運送会社との3社で、受発注から出荷・店舗配送まで一連の流れを全て調査し、分析しました。どこで滞留が起きているのか、などを明らかにしたものです。
⑥異業種との取り組み……2021年、花き業種と共同配送の実験検証
豊明の花き事業者と組んで、中部のホームセンターに納品されている鉢物用の棚付き台車を活用し、「お花と当社の商品を一緒に運ぼう」という発想で取り組みました。テストに終わりましたが、鉢物用の台車は非常に綺麗に洗浄されており、問題なく使用できました。
⑦メーカートラックを共同活用
当社がメーカーの倉庫の近傍までトラック便を出している場合、そのトラックを使ってメーカーの商品を運び、共同活用する取り組みで、これは現在も実施しています。
⑧面・段単位発注
パレットの積載情報をメーカーから頂いて、それに合わせた発注をしようとの取り組みです。1パレット48個積みなのに50個発注したら、1パレットと半端な2個が別に出るわけで確認が大変な手間になります。そこで、パレット単位またはその1段・1面の単位で発注するようにしました。導入はかなり進み、大手メーカーでは発注量の約80%で実践されています。もちろん少数発注が主のためできない商品もあり、線引きは発注担当者に委ねています。
下流の小売側との連携に残る課題が
最後に今後の課題として、下流の小売との連携の可能性についてお聞かせいただけますか?
今井氏 そうですね。当社から見た下流側の課題は、小売業への納品リードタイムの短さです。明日お届けするものは、前日の昼くらいまでに受注し、翌日納品になると思われるかもしれませんが、実際には当社は、当日の夜までにお得意様のセンターに納品しています。つまり、「当日受注・当日納品」が現実です。ただしそのセンターで夜間に店舗別に仕分けして、店舗に届くのは「翌日」になる、ということです。
このままでは適切な配車ができません。予想で前々日に車を確保しておくほかなく、蓋を開けたらトラックが足りなかったり、余ったり。どうしても多めの台数を用意せざるを得ず、博打に近い状態になっています。
小売でも加工食品を主に扱うスーパー業界では、リードタイム延長に理解が広まっており、現実に製配販連携が動き出していますが…。
今井氏 日用雑貨業界では、小売店側から提案されることはないので、我々卸側から交渉するしかありません。要望は出していますが、反応は企業によって大きく違います。中には理解して一緒に取組んでくださる会社もあれば、逆にもっとリードタイムを短くするように求めてくる会社もあります。日用雑貨品は腐るものではありませんから、不可能ではないと思うのですが…。
私としてはメーカー、小売とも連携して、サプライチェーン全体で一本のラインができれば理想だと思っているのです。
卸業界もここまで集約が進んだのですから、ライバルの卸同士でも連携し、束になって取り組んでいければいいのですが。
今井氏 実際には荷物を運んでいる物流会社が、各卸の荷を積み合わせて共同配送している例もあります。
はい、前回お話しいただいたトランコム社がその事例を紹介してくださいました。
今井氏 そうした方向をもっと考えないといけませんね。メーカーから卸、そして小売への流れをもっと連携させれば、さらなる効率化も可能だと思います。政府と一緒になって取り組む必要があるかもしれません。実際、当業界には納品時の付帯作業がまだまだあり、簡素化を一緒に考える余地は大いにあります。下流では当社が発荷主、小売が受荷主になりますが、受け側の対応で改善できる部分はとても大きいと思います。
たとえば、出荷シールに納品時の指示を入れているのだから、それを守ってくれなければ困ると納品先に言われることがありますが、現場作業者はつどそんな細かな指示を見て作業できる状態ではありません。現場の人たちがどれだけ苦労しているかを荷主企業は「もっと物流の現場を知るべきではないか」と私は強く思います。より風通しの良い環境を作って、ドライバーからもどんどん本音が聞けるようになれば、我々は効率化のヒントをもっと一杯得られるのではないでしょうか。
私自身、物流を「みんなが思ったことを口に出し、行動できる」、つまり「心理的安全性の高い職場」に変革していこう、と叫んでいるので、現場の声を聞き、現場をもっと知るべきだとの今井さんのご意見に大賛成です。また、日用雑貨業界の製配販サプライチェーンにおける一気通貫の連携にはまだ課題があるとのご指摘、よく理解できました。物流現場を知り尽くしたお立場からの問題提起を重く受け止め、この記事で関係者各位の理解が少しでも得られることを期待しています。本日はありがとうございました!
執筆者 菊田 一郎 氏 ご紹介
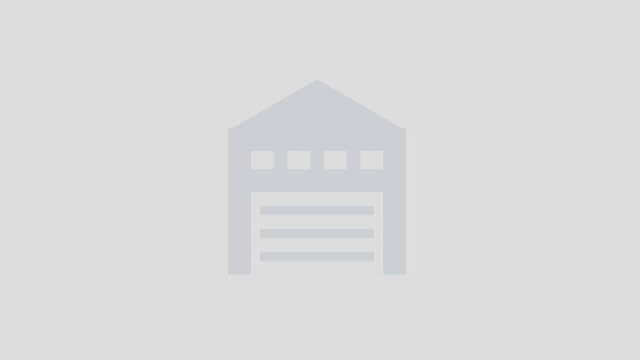
㈱大田花き 社外取締役、流通経済大学 非常勤講師、ハコベル㈱ 顧問
1982年、名古屋大学経済学部卒業。物流専門出版社に37年勤務し月刊誌編集長、代表取締役社長、関連団体理事等を兼務歴任。2020年6月に独立し現職。物流、サプライチェーン・ロジスティクス分野のデジタル化・自動化、SDGs/ESG対応等のテーマにフォーカスした著述、取材、講演、アドバイザリー業務等を展開中。17年6月より㈱大田花き 社外取締役、20年6月より㈱日本海事新聞社 顧問(20年6月~23年5月)、同年後期より流通経済大学非常勤講師。21年1月よりハコベル㈱顧問。
著書に「先進事例に学ぶ ロジスティクスが会社を変える」(白桃書房、共著)、ビジネス・キャリア検定試験標準テキスト「ロジスティクス・オペレーション3級」(中央職業能力開発協会、11年・17年改訂版、共著)など。
物流倉庫のご紹介
ロジスクエアふじみ野C
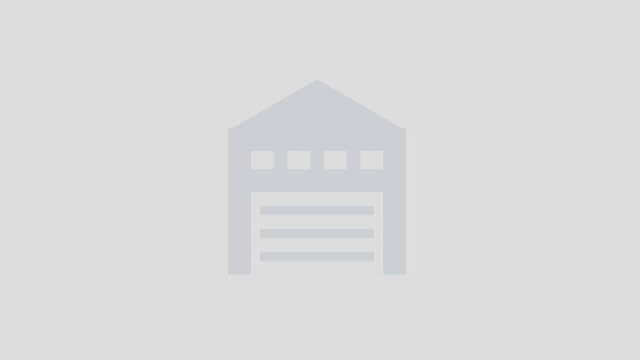
ロジスクエアふじみ野C棟は埼玉県ふじみ野市にて開発予定のBTS型物件です。
ふじみ野市は埼玉県の南部に位置しており、都心部へのアクセスにも優れ、物流拠点立地として県内でも有数のニーズの高いエリアです。開発予定地は道路ネットワークの活用により広域物流拠点立地としても優位性を備えています。
エリア別の募集中物件
関連サイト
サンスターグループ 荒木室長に聞く、日雑物流のリアル|物流クロスオーバー【日雑シリーズ 第1回】:
https://www.logi-square.com/interview/detail/240306
PALTAC物流キーマンに聞く、業界トップ卸の戦略|物流クロスオーバー【日雑シリーズ 第2回】:
https://www.logi-square.com/interview/detail/240417
トランコムの物流革新・共同化チャレンジ|物流クロスオーバー【日雑シリーズ 第3回】:
https://www.logi-square.com/interview/detail/240710